Chances are you don't have the equipment necessary to set up a security system just lying around, right? Well, you may be wrong. With only two computers - one with a webcam - and the Google Chrome browser installed on both, you have a rudimentary security system.
First, we'll set up the computer that will be connected to the webcam. Chances are this will be a laptop - because it seems that most - if not all - laptops these days have a built-in webcam. You should also be able to use a desktop or laptop with a USB webcam too, which might be ideal for placement purposes. On this computer, install
Google Chrome version 21 or above (version 21 includes support for a new API that allows the browser to access the webcam - don't worry, there's lot of warnings when you turn it on so you won't have someone spying on you without your knowledge). Once Chrome is installed, go to the
Chrome Remote Desktop BETA's Chrome Web Store link and install it (Note: This app requires at least Windows Vista or newer to work - for "security" reasons). Once it is installed, launch it and follow the simple steps to get it configured.
Now we will install Google Chrome on the viewer computer. The version does not specifically matter - as long as it can run the Remote Desktop app. Install
the same Chrome Remote Desktop BETA app on this computer and configure it as well. When you check out the app on the viewer computer, it will list your other computers along the bottom. Click on the cam computer you want to connect to and you will be prompted to enter the pin you set up when you configured the app. Open the
HTML5 Webcam Toy link on the cam computer and allow the site to connect to the webcam. You can now remotely view the webcam's video from another computer exclusively using Google Chrome - a program that doesn't require administrative rights to install. Have fun with it!
DISCLAIMER: Don't use this process to spy on things you shouldn't be looking at. I'm only posting this as a neat novelty use of technology. I will not be held responsible for any possible trouble you get yourself into using this technique.
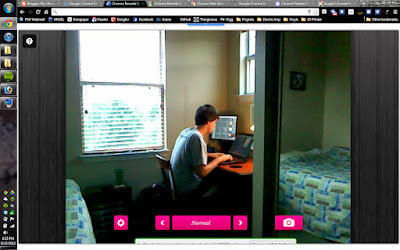 |
View on the viewer computer |
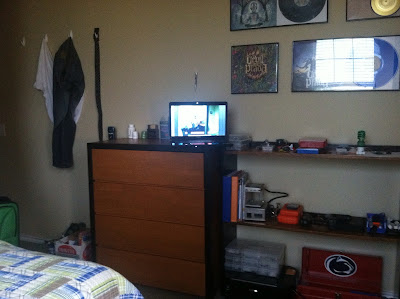 |
The cam computer is set up behind me |